In today’s interconnected world, the construction industry relies heavily on complex supply chains to ensure timely delivery of materials.
However, as recent events have illustrated, these chains are susceptible to disruptions. Understanding and managing supply chain delays has become an essential skill for every construction manager.
Let’s delve into the nature of these delays, their impacts, and ways to get ahead of them.
1. Understanding the Root Causes
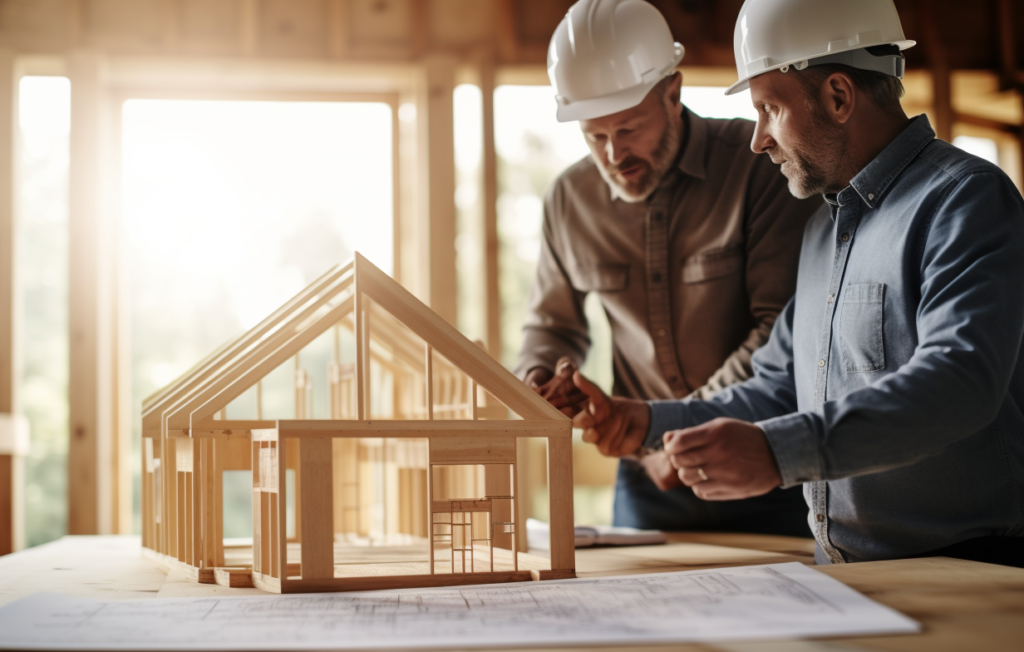
Supply chain delays arise from multiple sources that need to be closely tracked. Monitoring leading indicators from across the globe provides advanced insights.
- Natural disasters: Events like earthquakes, floods, or hurricanes can completely halt production or transportation for extended periods. Actively track weather forecasts and seismological readings in supplier regions for early warnings.
- Geopolitical factors: Tariffs, trade wars, government instability, and other political decisions can rapidly affect availability and pricing of materials. Continuously analyze new regulations and political developments that may disrupt flows. Keep an eye on new regulations and political climates globally.
- Economic shifts: Recessions, reduced production capacities, bankruptcies, and currency fluctuations can quickly lead to product scarcity. Closely follow macroeconomic trends and indicators to detect issues brewing. Watch for signs of economic downturns.
- Logistical bottlenecks: Limited transport availability, congested ports, driver shortages, and customs delays can abruptly slow deliveries. Routinely audit logistics channels across all modes of transport for bottlenecks. Audit logistics channels frequently for potential issues.
- Health crises: As seen during COVID-19, public health events can unexpectedly close factories for weeks and impact worker attendance. Monitor virus spread models and local health directives wherever suppliers operate. Keep up with developing health situations worldwide.
2. The Domino Effect on Construction
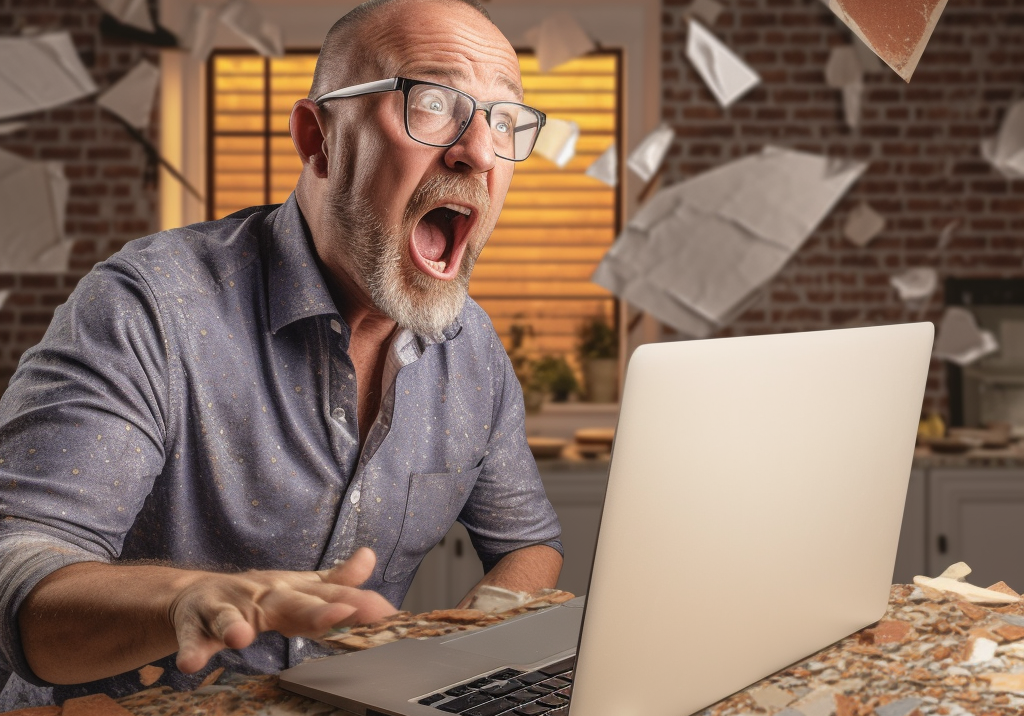
Delayed materials can unleash widespread disruptions across a construction project. Even minor delays can spiral into major cost and schedule overruns.
- Budget overruns: Storage fees, non-productive labor costs, rental fees for idled equipment, and price hikes for rush orders can explode budgets. A single day of delay can add significant unplanned costs.
- Missed deadlines: With tight schedules, even small delays can push back project milestones and completion dates, resulting in penalties. Deadlines often cascade, where one delay triggers a ripple effect on subsequent activities.
- Inferior quality: Rush material substitutions to stay on track further risk compliance issues and rework down the line. Last-minute purchases heighten the risks of unvetted products and defects.
3. Proactive Strategies to Mitigate Impact
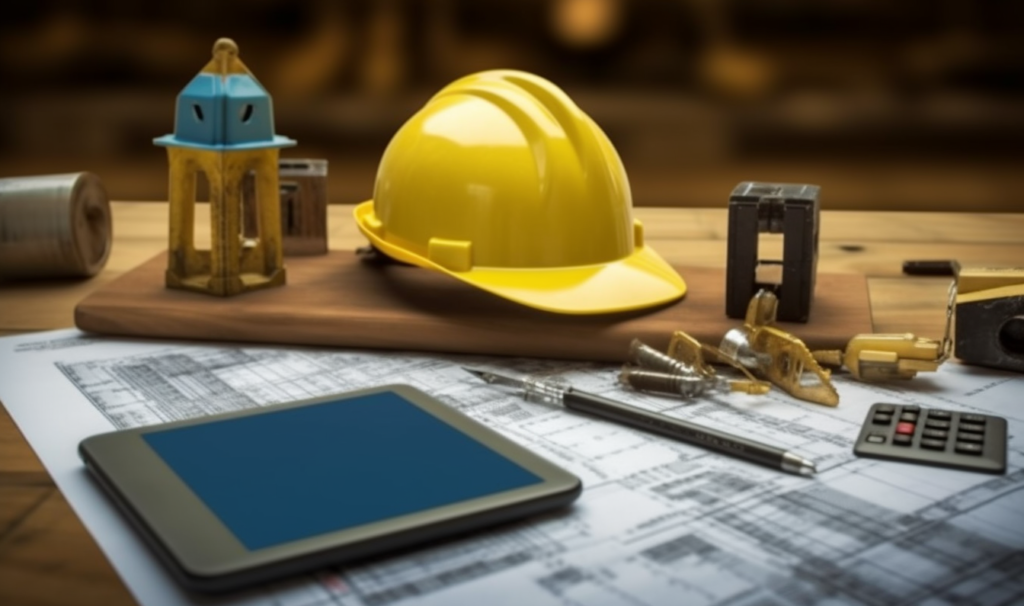
While supply chain shocks can’t be fully prevented, several tactics can reduce their damage. A diversified, flexible, and collaborative approach is key.
- Multi-source: Maintain relationships with redundant suppliers in various global regions to circumvent local disruptions. Always have backup sources to prevent over-reliance on a single supplier.
- Advance orders: Order far in advance and confirm production schedules to have a time buffer against delays. Build lead time estimates to demand spikes or slowdowns at factories.
- Safety stock: Maintain minimum on-hand inventory of critical materials to sustain operations during shortages. Determine optimal inventory levels for striking a cost vs. availability balance.
- Flexible contracts: Negotiate provisions in contracts to allow deadline extensions in case of supplier delays. Define clear force majeure clauses for qualifying events.
- Enhanced visibility: Mandate real-time tracking and status updates from suppliers for early problem detection. Integrate systems for access to supplier data.
4. Leverage the Latest Technologies
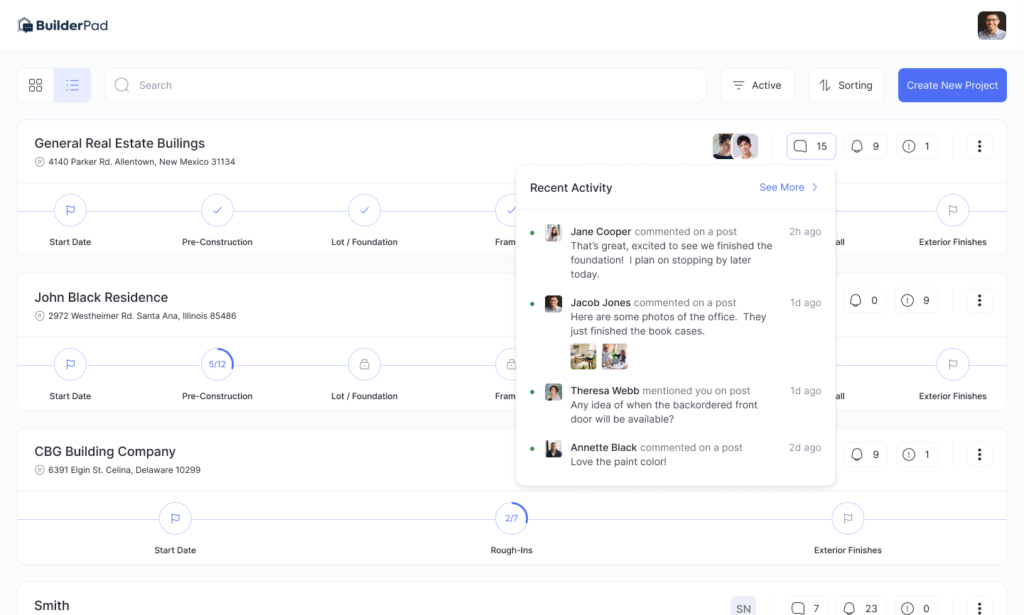
Modern solutions provide invaluable assistance in resilience. Digital tools enable predictive capacities and real-time coordination.
- Supply chain analytics: AI-powered analytics can detect early signals of potential supplier and logistics interruptions. Automated algorithms can rapidly parse disparate data feeds globally.
- Inventory optimization: Leverage data to minimize inventory costs while balancing availability. Analyze usage patterns and demand forecasts to determine ideal levels.
- Predictive scenario modeling: Run “what-if” simulations to evaluate and prepare for various supply chain scenarios. Stress test for worst-case disruptions to develop robust contingency plans.
- Digital collaboration: Platforms like BuilderPad enhance transparency in real-time between the construction site and suppliers to accelerate responses. Construction management platforms provide complete visibility across the supply chain. Leverage digital tools to collectively troubleshoot issues.
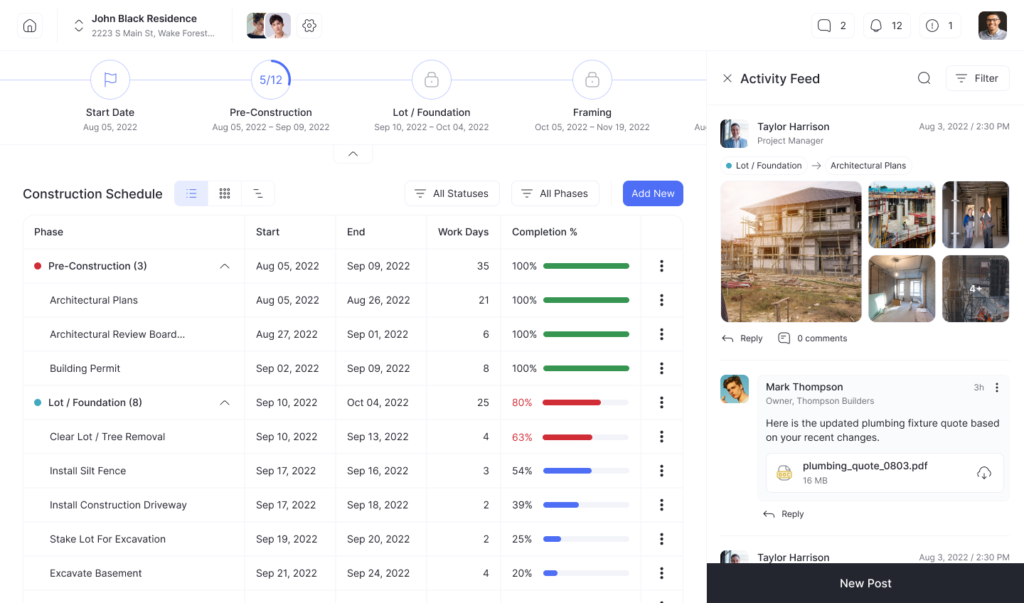
5. Learning to Shape the Future
Supply chain turmoil provides crucial lessons for the construction industry. Every disruption presents an opportunity for improvement.
- Build in buffers: Allow schedule and budget buffers to minimize impact of expected disruptions. Analyze past volatility to derive appropriate buffer sizes.
- Embrace agility: Nurture a flexible and adaptable culture focused on rapid response and creative problem-solving. Empower teams to make real-time decisions during disruptions.
- Obsess about readiness: Make contingency planning, scenario analyses, and early warning systems a priority. Dedicate personnel solely focused on monitoring for potential disruptions.
- Enable connectivity: Invest in digital platforms and data integration to enable end-to-end visibility and coordinated responses. Integrate systems across internal and external stakeholders.
Conclusion
Supply chain shocks are inevitable, but their damages can be mitigated through vigilance, preemptive strategies, and real-time visibility technologies like BuilderPad.
By bracing for potential disruptions and taking steps to boost resilience across the supply chain, construction firms can navigate delays smoothly and strengthen their capabilities for the future.
With comprehensive preparation, customer expectation management and collaboration, supply chain hiccups can be managed, and even transformed into catalysts for innovation.
Key Takeaways:
- Monitor leading indicators across suppliers, logistics, economics, and health to get ahead of potential disruptions.
- Build in schedule and budget buffers to allow flexibility during supply delays.
- Diversify sources, order early, and maintain safety stock of critical materials.
- Leverage supply chain analytics, simulations, and digital tools to enhance visibility and coordination.
- Learn from each disruption to improve resilience through buffers, flexibility, and integration.
With vigilance, contingency planning, and real-time supply chain visibility, construction firms can turn potential delays into opportunities to hone their responsiveness and emerge stronger.